Here Is A Quick Way To Solve A Tips About Is SCADA Same As DCS
Difference Between SCADA Vs DCS
SCADA vs. DCS
1. What's the Buzz About SCADA and DCS?
Ever feel like the world of industrial automation is just a giant bowl of alphabet soup? You hear terms like SCADA and DCS thrown around, and if you're anything like me, you might just nod politely and hope no one asks you to explain the difference. Well, fear not! We're about to dive into the world of Supervisory Control and Data Acquisition (SCADA) and Distributed Control Systems (DCS), breaking down what makes them tick (and how they differ) in plain, easy-to-understand language. Think of it as your friendly guide to demystifying industrial automation, without all the jargon.
So, where do we even begin? Let's start with the core concept: both SCADA and DCS are control systems used in various industries to monitor and control processes. They both involve computers, sensors, and actuators working together to automate tasks, improve efficiency, and keep things running smoothly. However, the devil, as they say, is in the details — and that's where the differences begin to emerge. Think of them as cousins in the automation family, sharing some DNA but ultimately having very different jobs and personalities.
Imagine a sprawling oil pipeline network stretching across hundreds of miles. A SCADA system would be ideal here. It's designed to monitor and control geographically dispersed assets, collecting data from remote locations and sending commands back as needed. Now, picture a complex chemical plant with interconnected processes happening in a relatively confined area. A DCS would be right at home here, providing precise, real-time control over individual processes and ensuring they all work together harmoniously. See the distinction? One's about wide-area monitoring, the other's about localized control.
Think of it like this: SCADA is the eagle soaring high above, keeping an eye on the big picture, while DCS is the diligent worker on the ground, meticulously managing the details. Both are essential for smooth operations, but they play very different roles. Grasping this fundamental difference is the first step to untangling the automation alphabet soup, so you can finally impress your colleagues at the next industry conference (or at least avoid that awkward silence when the topic comes up!).

SCADA
2. How SCADA Does Its Thing
Let's zoom in on SCADA for a moment. As mentioned earlier, SCADA systems are masters of long-distance communication. They typically operate over wide geographical areas, often using wireless communication technologies to connect to remote sites. This makes them perfect for industries like oil and gas, water and wastewater management, and electrical power distribution. Imagine a control center where operators can see the status of pumps, valves, and sensors located hundreds of miles away, all on a single screen. That's the power of SCADA!
A key characteristic of SCADA is its focus on data acquisition. SCADA systems gather vast amounts of data from remote devices, allowing operators to monitor trends, identify potential problems, and make informed decisions. Think of it as a giant data-collecting machine, constantly feeding information back to a central control center. This data is then used to generate reports, create visualizations, and trigger alarms when something goes wrong. For example, a SCADA system might alert operators to a sudden drop in pressure in a pipeline, allowing them to take corrective action before a leak occurs.
SCADA systems generally don't handle real-time control at the level of individual process loops. Instead, they focus on supervisory control, meaning they send setpoints and commands to local controllers, which then manage the fine-grained details. This distributed architecture allows SCADA systems to scale to very large sizes without being overwhelmed by the complexity of controlling individual processes. It's like having a general who issues orders to the troops, but doesn't get bogged down in every tactical decision on the battlefield.
However, its worth noting that cybersecurity is a major concern for SCADA systems. Because they often rely on open communication networks, they can be vulnerable to cyberattacks. Imagine a hacker gaining access to a SCADA system controlling a power grid — the consequences could be catastrophic. Therefore, robust security measures, such as firewalls, intrusion detection systems, and encryption, are essential for protecting SCADA systems from unauthorized access and malicious activity. Think of it like having a fortress with multiple layers of defense to protect your valuable data and critical infrastructure.
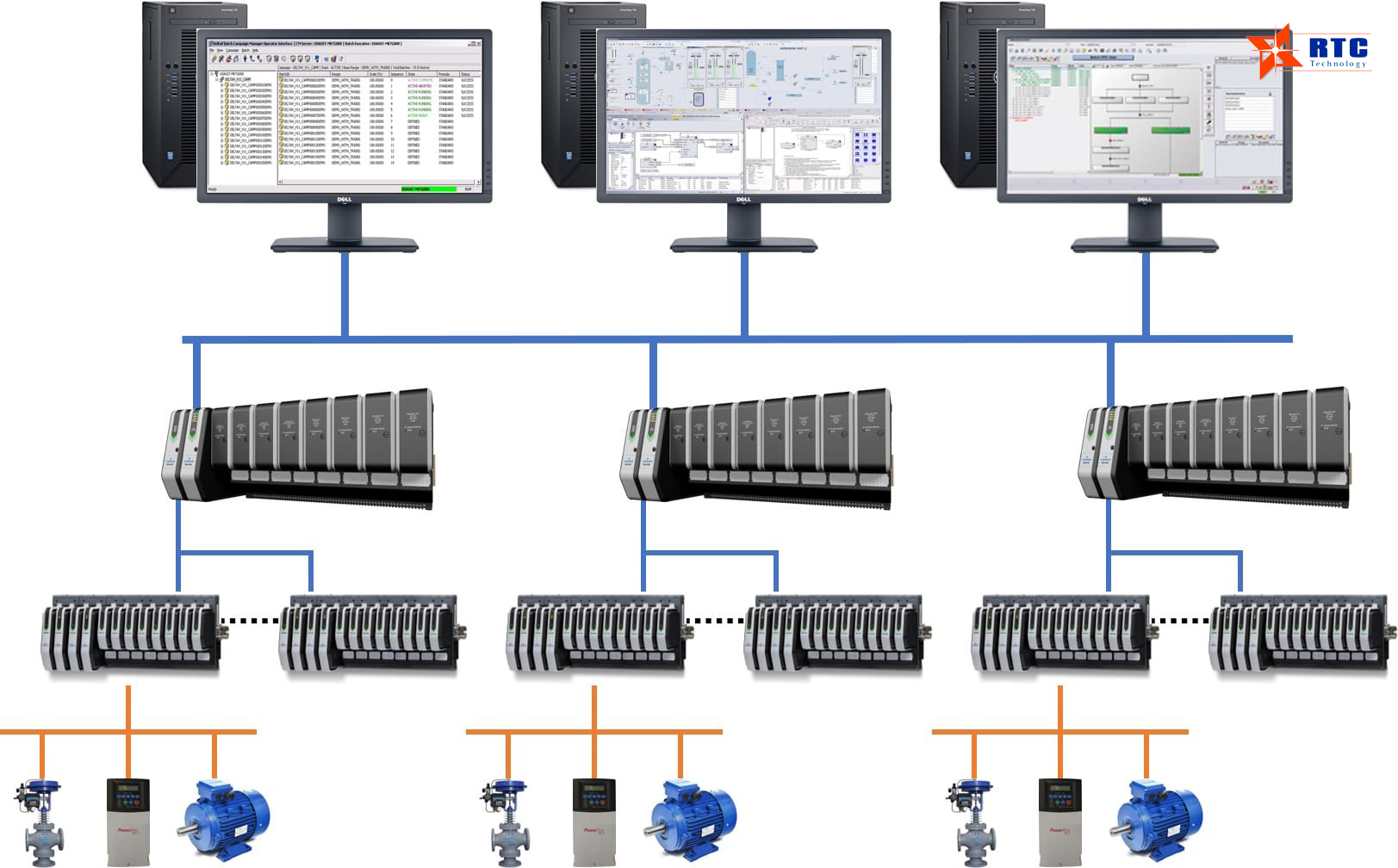
DCS
3. The Inner Workings of DCS
Now, let's shift our focus to DCS. Unlike SCADA, which spans vast distances, DCS is typically confined to a single plant or facility. It's designed to control complex, interconnected processes in real-time, with a high degree of precision and reliability. Think of industries like chemical manufacturing, pharmaceuticals, and food processing, where precise control over temperature, pressure, and flow rates is critical. A DCS is the maestro, orchestrating all the different instruments and sections of the plant to produce beautiful music (or, you know, a perfect batch of medicine).
DCS excels at managing closed-loop control, meaning it continuously monitors process variables and adjusts control outputs to maintain desired setpoints. This is achieved through sophisticated control algorithms and feedback mechanisms. Picture a thermostat in your home — it constantly monitors the temperature and adjusts the furnace or air conditioner to keep it within the desired range. A DCS operates on the same principle, but on a much grander scale, managing hundreds or even thousands of control loops simultaneously.
Another key feature of DCS is its integrated nature. All the components of a DCS, including controllers, I/O modules, and operator interfaces, are designed to work together seamlessly. This allows for tight coordination between different parts of the process and ensures that everything operates in harmony. It's like having a well-oiled machine, where every gear and lever works in perfect sync to achieve a common goal. This integration also simplifies troubleshooting and maintenance, as all the information you need is readily available in a centralized location.
Because DCS focuses on real-time control, it typically uses dedicated communication networks with high bandwidth and low latency. This ensures that control signals are transmitted quickly and reliably, minimizing delays and preventing process upsets. Think of it like a high-speed internet connection dedicated solely to controlling the plant — no buffering or lag allowed! This allows DCS to respond quickly to changes in process conditions and maintain stable operation, even in the face of disturbances.
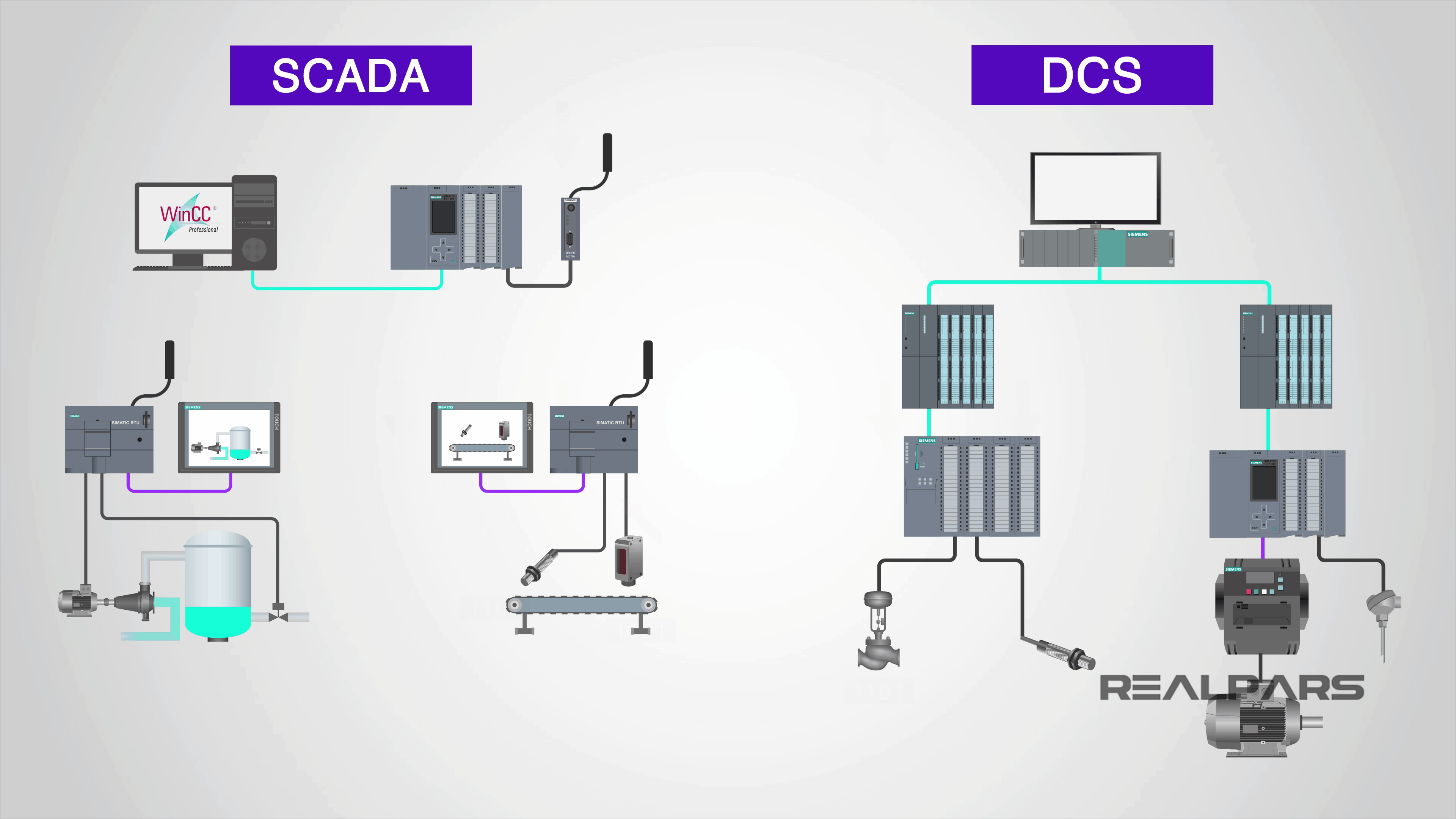
SCADA and DCS
4. Distinguishing the Two Systems
Alright, let's recap the key differences between SCADA and DCS in a way that sticks. We've talked about geographical scope, control philosophy, and communication networks. Let's distill this into a handy comparison chart:
- Geographical Scope: SCADA = Wide area; DCS = Localized
- Control Philosophy: SCADA = Supervisory control; DCS = Direct, real-time control
- Communication Networks: SCADA = Often uses public networks; DCS = Typically uses dedicated networks
- Data Focus: SCADA = Data acquisition and monitoring; DCS = Process control and optimization
Think of it like choosing between a telescope and a microscope. A telescope (SCADA) lets you see far-off galaxies, while a microscope (DCS) lets you examine the intricate details of cells. Both are valuable tools, but they serve different purposes. Understanding these fundamental differences is crucial for selecting the right control system for your specific application.
But, what if you need both wide-area monitoring and precise local control? In some cases, the answer is to integrate SCADA and DCS systems. This can be achieved by connecting a SCADA system to a DCS system, allowing operators to monitor and control the entire operation from a central location. However, this integration can be complex and requires careful planning to ensure that the systems work together seamlessly. It's like combining the best of both worlds, but you need to make sure they play nice together!
Ultimately, the choice between SCADA and DCS depends on the specific requirements of the application. There's no one-size-fits-all answer. Consider the geographical scope, the control requirements, and the communication infrastructure. By carefully evaluating these factors, you can choose the control system that best meets your needs and helps you achieve your automation goals. It's all about picking the right tool for the job, so you can get the most out of your automation investment.
Now, go forth and confidently discuss SCADA and DCS with anyone, knowing you've got a solid grasp of the basics. You're no longer lost in the alphabet soup!
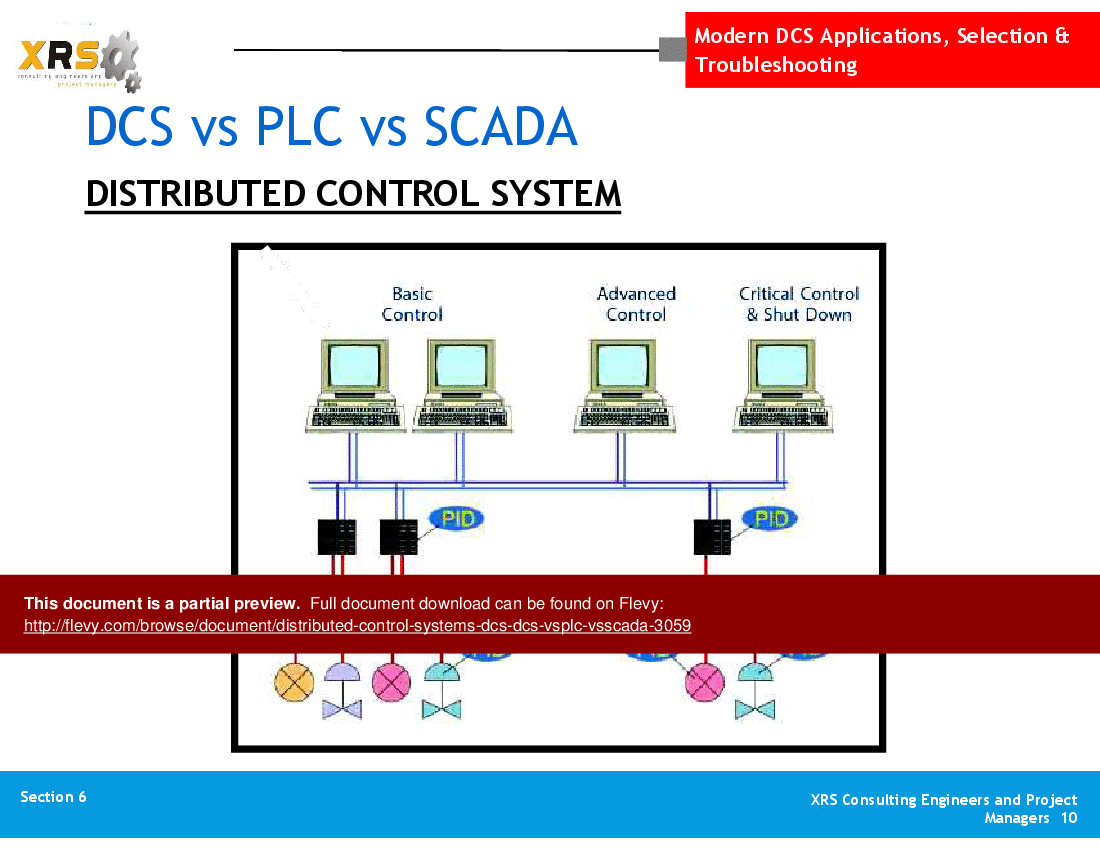
When SCADA and DCS Collide
5. The Best of Both Worlds?
Sometimes, the lines between SCADA and DCS become blurred. What happens when you need both wide-area monitoring and precise, real-time control? That's where integration and hybrid systems come into play. Imagine a large-scale water treatment plant that has remote pumping stations (SCADA territory) but also intricate chemical processes within the plant itself (DCS domain). Integrating these systems allows operators to oversee the entire operation from a single platform, gaining a holistic view of the process.
Integration can involve connecting a SCADA system to a DCS system, allowing data to flow between the two. This enables operators to monitor the performance of the entire operation, from the remote outstations to the individual process loops. Think of it as building a bridge between two islands, allowing traffic (data) to flow freely between them. This integration can be complex, requiring careful planning and execution to ensure that the systems work together seamlessly. Proper communication protocols and data mapping are crucial for a successful integration.
In some cases, hybrid systems are designed from the ground up to incorporate both SCADA and DCS functionalities. These systems often use a modular architecture, allowing users to select the components that best meet their needs. Think of it as building a custom-designed control system that combines the strengths of both SCADA and DCS. This approach can provide the flexibility and scalability needed to address complex automation challenges.
However, integrating SCADA and DCS systems also presents challenges. Security is a major concern, as connecting systems can create new vulnerabilities. Data management can also be complex, as data from different systems may need to be harmonized. It's essential to address these challenges proactively to ensure that the integrated system is secure, reliable, and easy to use. Careful planning, robust security measures, and a clear understanding of the data flows are essential for a successful integration.
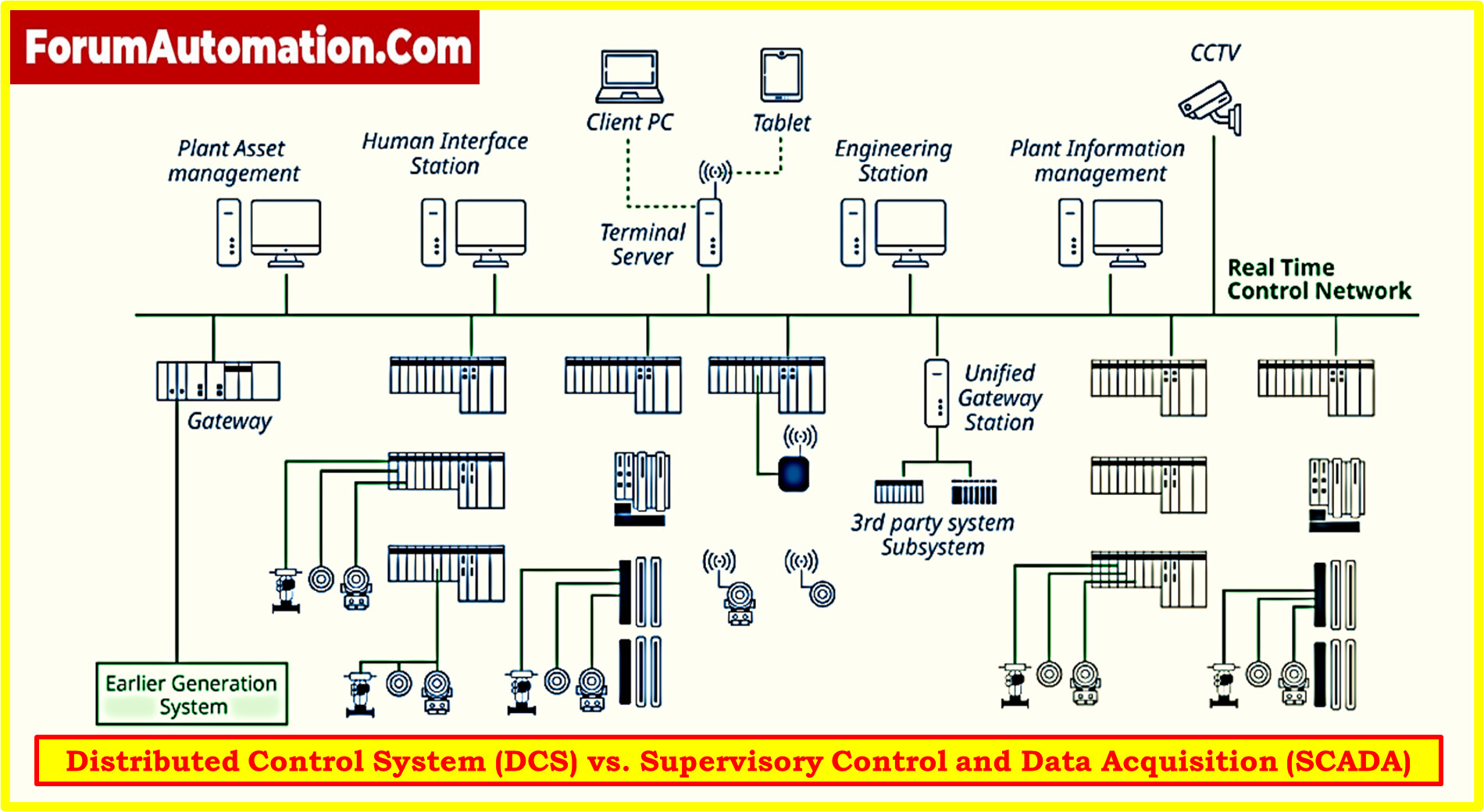
FAQs
6. Clearing Up the Confusion
Still a little unsure about something? Don't worry, here are some frequently asked questions to help clear up any lingering confusion:
Q: Is one system "better" than the other?
A: Nope! It's not about better or worse, it's about appropriate. SCADA is better for wide-area monitoring, DCS is better for localized control. It all boils down to your specific needs and application.
Q: Can I use SCADA for everything?
A: While SCADA can be used in a wide range of applications, it might not be the best choice for processes requiring very precise, real-time control. In those cases, a DCS is usually a better fit. Imagine using a hammer to tighten a tiny screw — it might technically work, but you're more likely to strip the threads. Choose the right tool for the job!
Q: Are SCADA and DCS the only control systems out there?
A: Not at all! There are other types of control systems, such as Programmable Logic Controllers (PLCs) and Human-Machine Interfaces (HMIs). These systems can be used independently or in conjunction with SCADA and DCS to create a complete automation solution. The world of industrial automation is vast and varied, with a tool for every task.