Underrated Ideas Of Tips About What Is BOM Abbreviation In SAP

Unlocking the Mystery of BOM in SAP
1. Deciphering the BOM Code
Ever stumbled across the abbreviation "BOM" while navigating the SAP landscape and felt a little lost? You're not alone! BOM stands for Bill of Material, and in the world of SAP, it's a pretty big deal. Think of it as a recipe for your products, but instead of flour and sugar, it lists all the components, raw materials, and sub-assemblies needed to create a finished item. It's the backbone of production planning and control, ensuring everything comes together smoothly.
But why is it called a "Bill"? Well, it essentially provides a detailed list, or "bill," of all the items that make up a product. Back in the day, these lists were probably actual paper bills! Thankfully, SAP has digitized the process, making it much easier to manage these complex relationships between materials. No more sifting through mountains of paperwork!
In simpler terms, imagine you're building a LEGO castle. The BOM is like the instruction manual, telling you exactly which bricks you need and how they fit together. Without it, you'd be stuck with a pile of colorful plastic and a whole lot of frustration. Similarly, in manufacturing, the BOM ensures that all the necessary components are available when needed, preventing costly delays and keeping production on track.
So, whether you're dealing with nuts and bolts, electronic components, or even packaging materials, the BOM in SAP is your go-to resource for understanding the composition of your products. It's the unsung hero that keeps the wheels of manufacturing turning!

SAP PP BOM Active Version & Inactive Check... Community
Why Should You Care About BOMs in SAP? (A Few Compelling Reasons)
2. The Importance of Mastering the BOM
Okay, so now you know what BOM stands for, but why should you, as someone navigating the SAP ecosystem, actually care about it? It's more than just knowing a piece of jargon; understanding BOMs can significantly impact various aspects of your work and the overall efficiency of your organization. Think of it as unlocking a secret level in the SAP game!
First and foremost, accurate BOMs are crucial for efficient production planning. Imagine trying to plan production without knowing exactly what materials you need. It'd be like trying to bake a cake without a recipe — you'd likely end up with a disaster! A well-maintained BOM ensures that the right materials are available at the right time, minimizing stockouts and preventing production bottlenecks. This leads to smoother operations and happier customers (and who doesn't want happy customers?).
Furthermore, BOMs play a vital role in cost control. By accurately tracking the components and quantities required for each product, you can gain a clear picture of the true cost of manufacturing. This information is essential for making informed pricing decisions and identifying opportunities for cost reduction. Think of it as having a detailed breakdown of all your expenses, allowing you to pinpoint areas where you can save money. Every little bit counts!
Beyond planning and cost control, BOMs are also essential for engineering change management. When a product design changes, the BOM must be updated to reflect the modifications. This ensures that the correct components are used in the revised product and that any obsolete materials are properly managed. It's all about keeping everything synchronized and preventing costly errors. Basically, it keeps you from accidentally building the wrong version of your product!
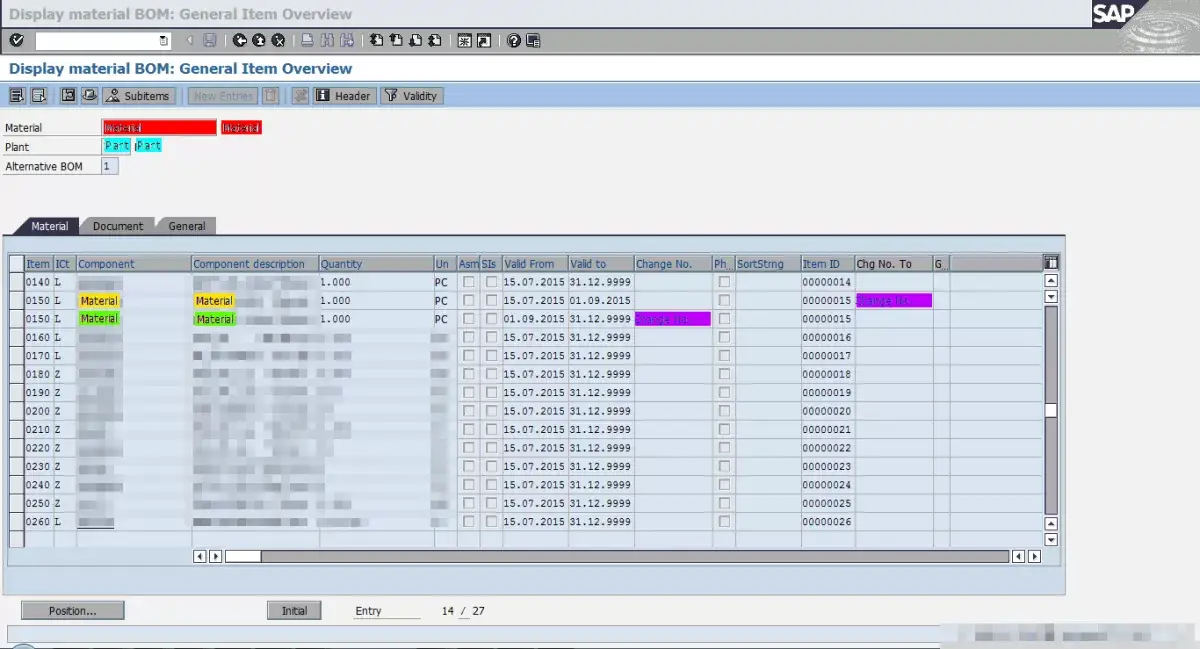
Different Flavors of BOMs
3. Exploring the BOM Universe
Just like there are different flavors of ice cream, there are also different types of BOMs in SAP. While the core concept remains the same — a list of materials needed to create a product — the specific type of BOM used can vary depending on the industry, the complexity of the product, and the specific business processes involved. Understanding these variations is crucial for working effectively with BOMs in SAP.
One common type is the Manufacturing BOM, which focuses on the materials and components required for the physical manufacturing process. This type of BOM typically includes details such as quantities, units of measure, and the sequence of assembly operations. It's the go-to BOM for production planning and shop floor control.
Another variation is the Engineering BOM, which is often used during the product design phase. This type of BOM may include additional information such as design specifications, CAD drawings, and other engineering-related data. It serves as a central repository for all the technical information related to a product.
Then there's the Sales BOM, which is used to configure products at the point of sale. This type of BOM allows customers to select specific options and features, and the system automatically generates a BOM that reflects the customer's choices. Think of it as building your own custom PC online — the Sales BOM ensures that all the selected components are compatible and can be assembled into a working system.
Knowing which type of BOM you're dealing with is essential for interpreting the information correctly and using it effectively. It's like understanding the difference between a recipe for baking a cake and a recipe for grilling a steak — using the wrong recipe can lead to a disastrous outcome!
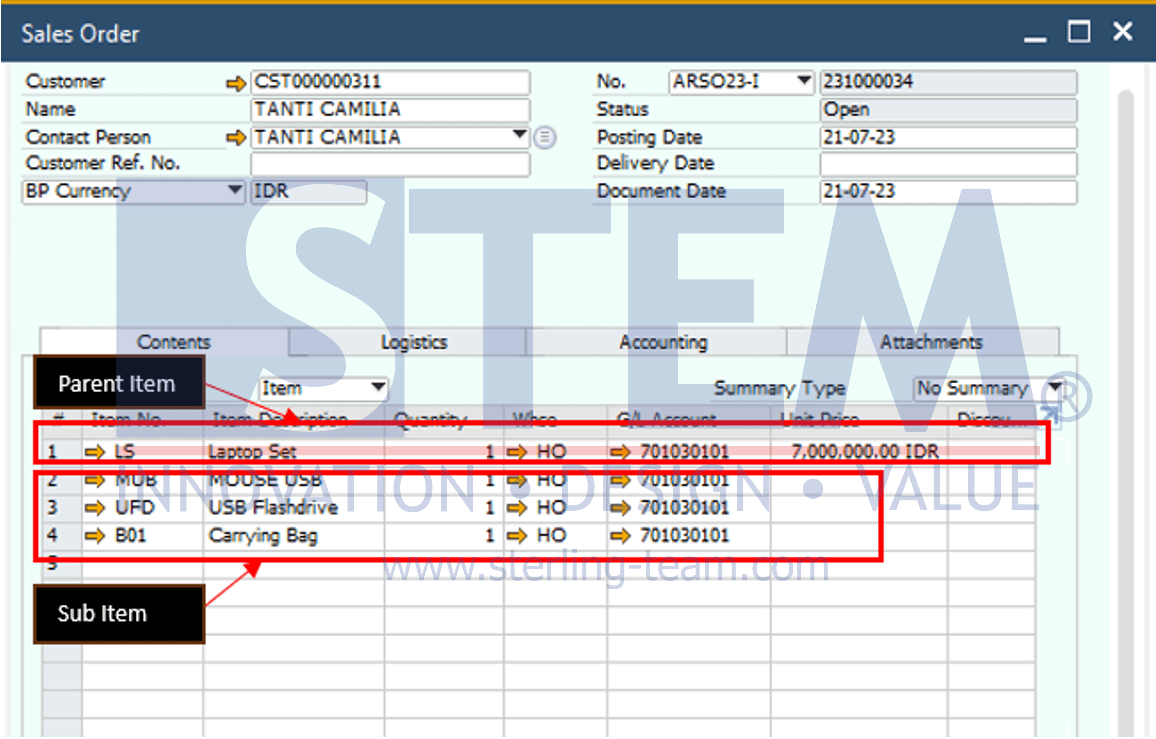
Navigating the BOM in SAP
4. BOMs in Action
Alright, now that we've covered the theory, let's get practical. How do you actually work with BOMs in SAP? Fortunately, SAP provides a range of transactions and tools for creating, maintaining, and using BOMs. Mastering these tools is essential for anyone who works with product data in SAP.
One of the most fundamental transactions is CS01, which is used to create a new BOM. This transaction allows you to specify the material for which you are creating the BOM, the plant where the BOM is valid, and the usage of the BOM (e.g., manufacturing, engineering, sales). It's the starting point for building your product recipe in SAP.
Once you've created a BOM, you can use transaction CS02 to change it. This transaction allows you to modify the components, quantities, and other attributes of the BOM. It's essential for keeping your BOMs up-to-date as product designs and manufacturing processes evolve. Think of it as constantly tweaking your recipe to make it even better!
To display an existing BOM, you can use transaction CS03. This transaction provides a read-only view of the BOM, allowing you to see the components, quantities, and other details. It's a quick and easy way to check the composition of a product.
Beyond these basic transactions, SAP also offers a range of reporting tools for analyzing BOM data. These tools allow you to identify potential issues, such as missing components or incorrect quantities, and to optimize your BOMs for cost and efficiency. It's like having a powerful analytics dashboard that helps you fine-tune your product recipes for maximum performance!
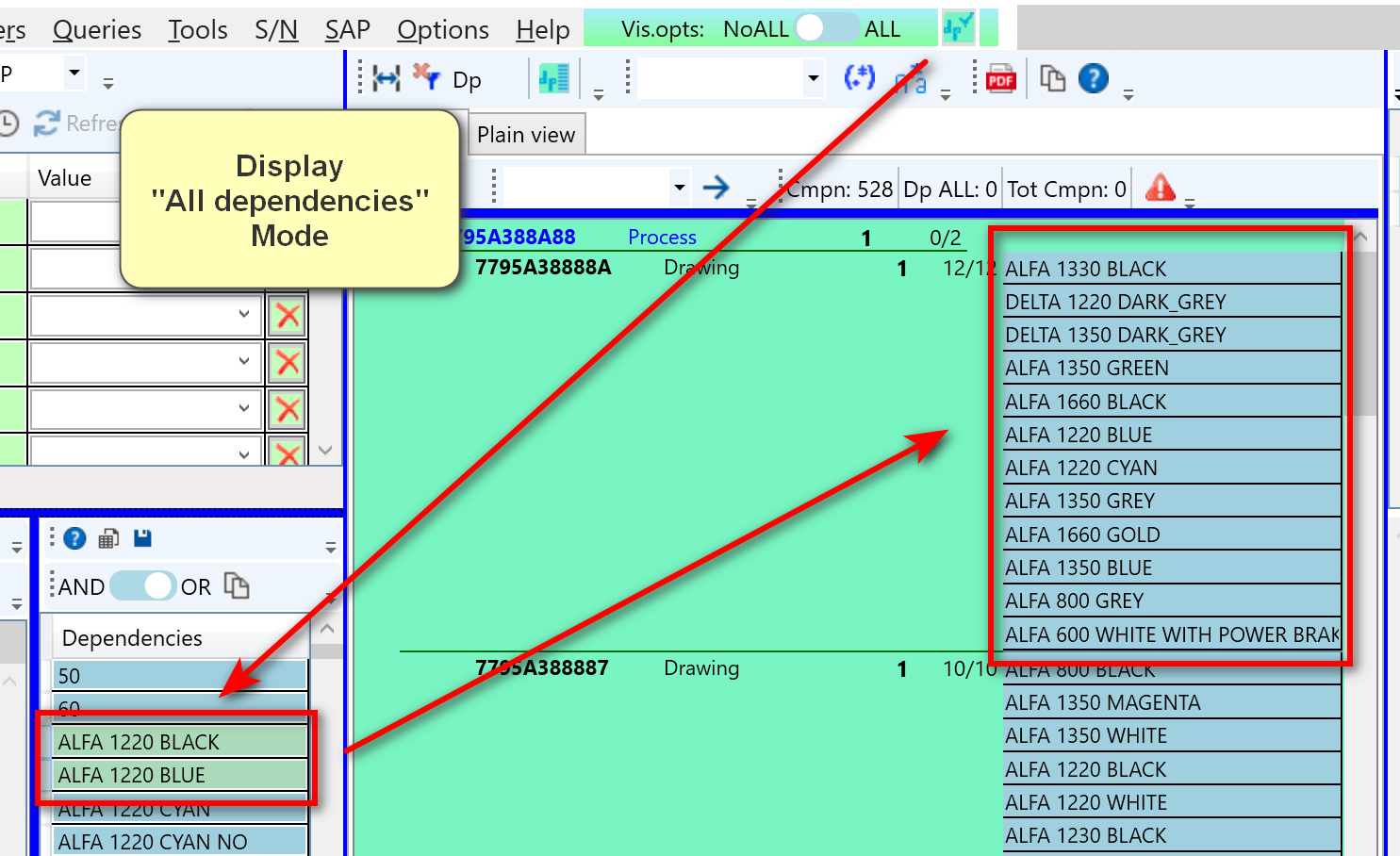
6 BOM Analyzer MultiLevel Visual For SAP
Common BOM Challenges (and How to Overcome Them)
5. Tackling BOM Troubles
Working with BOMs in SAP isn't always a walk in the park. Like any complex system, there are challenges that you're likely to encounter along the way. Being aware of these challenges and knowing how to overcome them is crucial for maintaining accurate and reliable BOM data.
One common challenge is maintaining data accuracy. BOMs can become outdated quickly if changes aren't properly documented and updated in the system. This can lead to errors in production planning, material procurement, and costing. The key to preventing this is to establish clear processes for managing engineering changes and ensuring that BOMs are updated promptly. Think of it as having a strict version control system for your product recipes.
Another challenge is managing BOM complexity. Some products can have hundreds or even thousands of components, making it difficult to track and manage all the relationships. In these cases, it's important to use SAP's BOM management tools effectively, such as phantom assemblies and multiple BOMs, to simplify the structure and improve maintainability. It's like breaking down a complex recipe into smaller, more manageable steps.
Finally, ensuring BOM consistency across different departments and systems can be a challenge. Different departments may have different views of the BOM, leading to inconsistencies and errors. The key to addressing this is to establish a single source of truth for BOM data and to ensure that all departments are using the same definitions and standards. It's all about getting everyone on the same page and speaking the same language when it comes to product data.
By proactively addressing these challenges, you can ensure that your BOMs in SAP are accurate, reliable, and contribute to the overall efficiency of your organization.
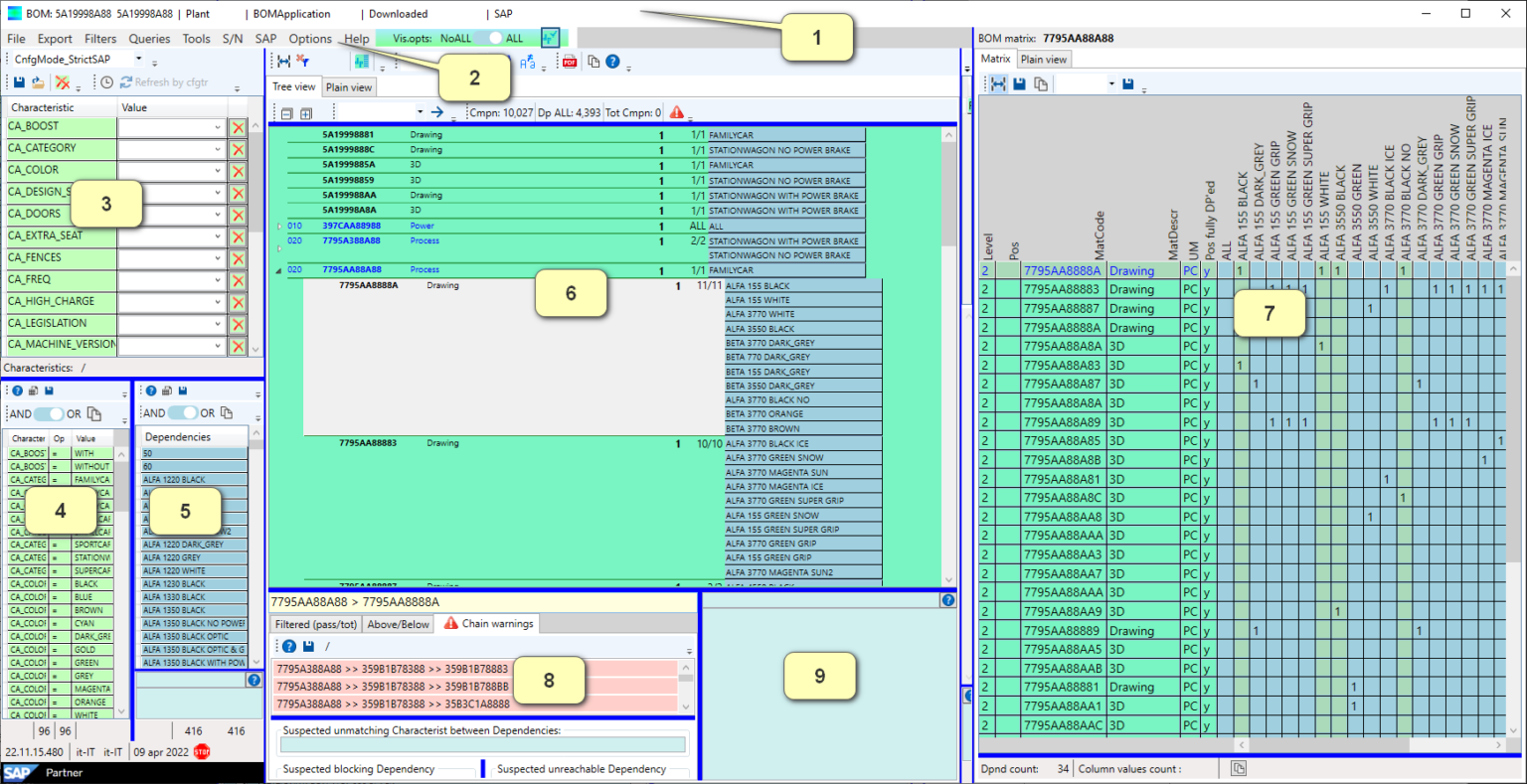
BOM Analyzer Interface Introduction Visual For SAP
FAQ
6. Everything You Wanted to Know (But Were Afraid to Ask)
Q: What's the difference between a single-level BOM and a multi-level BOM?
A: A single-level BOM shows only the direct components of a finished product. A multi-level BOM, on the other hand, shows the entire hierarchy of components, including sub-assemblies and their constituent parts. Think of it like this: a single-level BOM is like a simple ingredient list, while a multi-level BOM is like a detailed recipe with sub-recipes for each component.
Q: How do I handle obsolete components in a BOM?
A: When a component becomes obsolete, you should mark it as inactive in the BOM and replace it with a new component. You'll also want to ensure that any remaining inventory of the obsolete component is properly managed. SAP provides tools for managing obsolete materials and ensuring that they are not used in future production runs. It's like cleaning out your pantry and replacing expired ingredients with fresh ones.
Q: Can I use BOMs for services, not just physical products?
A: While BOMs are primarily used for physical products, you can also use them to represent the components of a service. For example, a BOM for a consulting service might include the number of hours required for each task, the skill level of the consultant, and any other resources needed to deliver the service. It's all about breaking down the service into its constituent parts and managing them effectively.
Q: What is a phantom assembly in SAP BOM?
A: A phantom assembly is a temporary grouping of components within a BOM that are treated as a single unit for planning purposes but are not actually stocked as a separate item. Imagine constructing a cake, the frosting itself not counted, but part of cake itself.